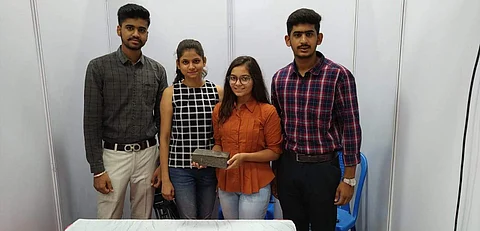
Did you know that India, the second largest producer of bricks in the world, makes around 200 billion bricks a year? As good quality soil is preferred as raw material for making bricks and the number of brick producing units in the country is estimated to exceed 100,000, it is approximated that the brick industry consumes around 400 million tons of good quality soil every year! Also, the burning of fuel for firing bricks results in emissions of gaseous pollutants and ash into the environment causing air pollution.
Keeping this in mind, a group of students from Udaipur has come up with a new and envirosafe idea to make bricks from domestic and industrial waste, calling it ‘Wricks’. The start-up comprises of Kunjpreet Kaur Arora, Krishna Chaudhary, Daidipya Kothari and Honey Singh Kothari who are civil engineering students from Techno India NJR Institute of Technology, Udaipur. They use plastic waste, marble waste, demolition waste and thermal waste as the raw material instead of soil.
“This idea popped when we looked at our college ground which was covered with plastic bottles. Being civil engineering students, we thought of using it for something useful,” says Kunjpreet. The team researched about this for a year — under the guidance of their professors — to come up with a prototype that contains 30-40 per cent of plastic waste, 40-50 per cent of demolition waste and 20 per cent of marble waste and thermal waste. These “Wricks’ also contain marble slurry as its component. “Many lakes near Udaipur are getting polluted and the municipality is still figuring out a way to manage marble slurry waste. That’s when we thought of including it as well,” says Kunjpreet Kaur Arora.
It is no surprise that the process of making traditional bricks causes air pollution. But ‘Wricks’ not only uses waste as the raw material but also has a very environment-friendly manufacturing process. “We have come up with an environment-friendly technology that will significantly reduce air pollution and manage waste effectively. There are no residues left, no carbon emission and no by-products formed,” says Kunjpreet. These ‘Wricks’ are also manufactured insanely fast — they can produce about 100-120 bricks per hour at just ₹3 per brick.
But can these ‘Wricks’ actually replace the red clay bricks available in the market? In fact, the initial test results have shown that ‘Wricks’ is technically superior to bricks. It has good compression strength and they are non-porous. It has only 1-2 per cent water absorption capacity, while traditional bricks have 20 per cent, hence creating problems like Efflorescence. It has also passed tests like soundness and hardness where the results are on par with first-class red clay bricks. “People who need lightweight bricks to be used in the construction of high rise commercial buildings will find ‘Wricks’ tailor-made for them,” says Kunjpreet.
Also, this idea is aimed for the welfare of the community and they have estimated the price of the final product without keeping the profit in mind. “As you can observe, our day to day activities produce a huge amount of waste and no one knows how to reduce and reuse it properly. We also rely on red clay bricks that cause air pollution and soil erosion. If we sell 10 lakh 'Wricks', it will recycle 2,50,000 kg of waste material in all categories.” says Kunjpreet.
The government authorities, municipality and UIT at Udaipur were also very impressed by this start-up. They will commercialise this product once it is certified by the government laboratories and will launch it by 2020. They are planning to scale-up by introducing lightweight reinforced panels, tiles and many more products in the future.