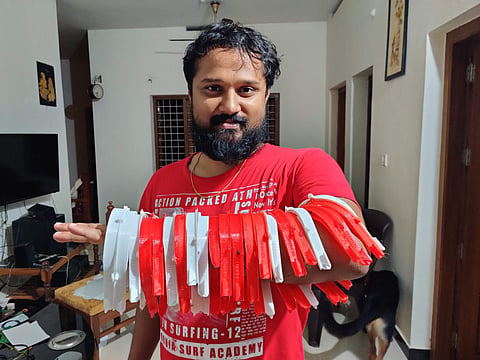
When Manu Krishnan heard from one of his friends that there is an acute shortage of face shields at hospitals in Kerala, he decided to do something about it. A Mechanical Engineer at Continental Automotive in Bengaluru, Manu decided to design an effective face shield and provide them to healthcare workers free of cost and he made them biodegradable too, although not on purpose. ”Since, designing products is my forte, I decided to use my skills to design a face shield. I didn't, however, aim to make them bio-degradable as the idea was to deal with the shortage of face shields at first,” says Manu, who is originally from Kerala and who returned to his homeland when the government announced the lockdown.
Manu, along with his younger brother took the help of the Emergency Response Team to procure materials from Ernakulam. “They procured a large number of polycarbonate sheets and polylactic acid (PLA) bands (made from sugars of corn starch). These sheets are biodegradable because of the presence of EcoPure additives in them. They can be buried in the soil for bio-degradation but due to the high chances of the presence of the coronavirus on the mask, they are being burnt in incinerators at hospitals.” The 28-year-old engineer worked day and night to first develop the software. And that's what's unique about Manu’s work. He explains, “We downloaded an open-source G-CORE software online. Since our existing printer was different from others, we added other elements and tweaked the parameters in the software using Python. So, the software is, in a way, our own.”
Soon after they started printing biodegradable 3D sheets, Manu made a few face shields and gave it to the doctors to try out. But the bands were tight and the measurements turned out to be wrong. “I received a lot of criticism from healthcare officials. I then worked day and night to adjust the measurement and came out with a final product. Initially, I printed 50 of them and doctors were happy to wear them this time.” Manu started getting orders in large numbers but he was unable to meet the requirement without the help of a better printer. “We needed to make these shields in large numbers, probably 150 shields a day. This led me to create my own machine out of existing parts available around me, including parts from a Maruti car. Now, with the help of this machine, we can produce 150 shields a day. Recently, a surgeon had requested for disposable shields for the Operation Theatre. We produced more than 100 such shields in a day and delivered them on time,” explains Manu who has taught his parents to make the product as well so that they can continue to make the shields even after he returns to Bengaluru post-lockdown and sell each for `50.