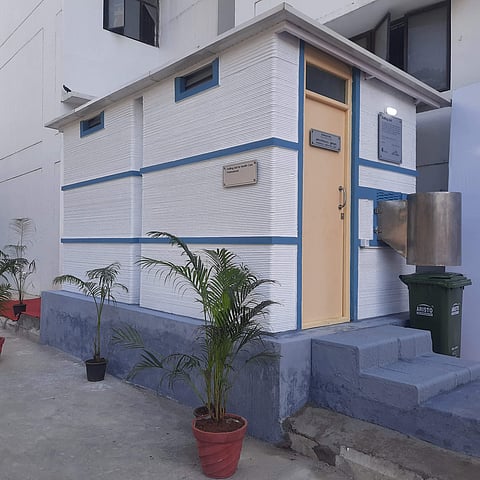
A start-up founded by alumni of IIT Madras has created a Doffing Unit — which will help doctors treating COVID-19 patients dispose PPE kits sans contact — using concrete 3D printing technology. The project was done by Tvasta, in collaboration with France-based manufacturing multinational company, Saint Gobain, and two of the three proposed Doffing Units have already been installed at Government Hospital in Kancheepuram and Omandurar Medical College and Hospital, Chennai. The third unit is set to come up at Government Medical College and Hospital in Tiruvallur.
Tvasta is a “deep-tech” start-up that specialises in concrete 3D printing. It was set up in 2016 when Adithya VS, Chief Executive Officer, Vidyashankar C. Chief Operating Officer and Parivarthan Reddy, Chief Technology Officer, were just out of college. They were in the news this year when they created India’s first 3D printed house at IIT Madras. That is where Saint Gobain came to know about them, and brought the guys on board for this CSR initiative.
So, what is a Doffing Unit, and what exactly makes this one created by the youngsters at Tvasta so ergonomical? Speaking with Edexlive, Parivarthan claims that these Doffing Units are the need of the hour, given the devastating nature of the pandemic. Essentially, Doffing units are rooms inside hospitals where healthcare providers can dispose of their Personal Protection Kits after a day of treating COVID patients. “However, the units we traditionally have, come with a risk of transmission. The PPE kits are disposed of in a dustbin in the room, which comes with a chance of transmission,” says Reddy. The unit, designed and 3D printed, by these youngsters has two separate exits, and comes with a chute where doctors can discard their PPE kits. The chute delivers in a covered dustbin outside, from where it is later cleared. Once they have discarded the kit, they can use the non-contact soap dispensers and sanitisers to clean their hands. Then they move into an inner room that contains a shower.
“The units are also equipped with a UV sanitisation box where doctors can place their change of clothes, phones and wallets for sanitising and safe use. They then leave through the specified exit, so there is negligible contact with any possible germs. Every step is put in place to minimise the risk of transmission,” says the 28-year-old.
Constructing the unit is a process that takes around 17 days. The unit is printed in separate parts, the 3D models of which are uploaded on the computer and then generated in concrete using the in-house 3D printer at Tvasta. The machine and the software both were developed by these engineers. This process takes four days. The parts are then left to “cure” for seven days in order for the concrete to set. They are then transported to the site, the hospitals in this case, and assembled across two-to-three days. “Time and cost, both are reduced significantly in this process, but most importantly, construction workers are saved from long exposure to COVID-19 at the hospitals,” says Parivarthan.
The engineer understands that there remains the challenge of scaling for this relatively new technology in the construction business, but he says that interest has been bubbling encouragingly over the last few months. “We have been getting queries from builders about this construction technology, and now the goal is to collaborate with possible partners, teach people about the technology and make it accessible. Housing will always remain a primary need for everyone, and so this technology can definitely go places in the coming years,” signs of Parivarthan.