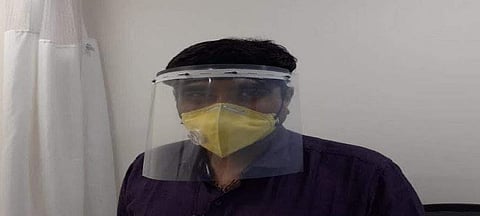
The Coronavirus outbreak and the lockdown that followed its rise have brought to light a number of horrifying accounts from health professionals. In their attempt to help those infected by the virus, they face the threat of the virus themselves and the stigma that surrounds it. As protective equipment grow vital for them, the management at Dayananda Sagar University challenged their academicians to use the available resources to solve this growing challenge.
It did not take long for the experts at the Autodesk Design and Innovation Centre, incubated at DSU to come up with a solution. They invented a face shield, one of the most vital personal protection equipments. The shield was developed by Vinayaka K, the Manager of Autodesk, Dr Suryanarayana, a Professor of Aerospace Engineering at the university along with Ajay P, a student of Automobile Engineering. It was manufactured using Fused Deposition Modelling, a 3D printing process that uses a filament of a thermoplastic material called Polylactic Acidas. It was first launched on March 28 and was available for use from March 31.
Currently, a number of units have been 3D printed by the university’s team. They are seeking the approval from the Indian Council of Medical Research (ICMR) as a medical device, for supply to the healthcare sector and other sectors fighting the COVID-19 pandemic. Following this, the idea is to mass produce the face shields for a minimal cost and make it widely available.
Dr Suryanarayana says, “The face shield has two main components: a support frame and a transparent film. The film can be easily attached and held at the frame. The shield itself can be easily worn by the health professionals. Transparency of the front film enables the wearer to interact with the patients in close proximity and continue to be safe. The film is disposable, can be discarded or easily replaced. It can also be reused after proper sanitisation.
Vinayaka K adds, “The aim is to give medical professionals extra coverage and protection. As a lot of them work who in close proximity with patients, the requirement of such safeguards continue to grow.” The team has already received multiple orders for the product and are continuously working out for ways to enable mass production of it even at this time of limited access to resources and technology. Autodesk is supported by Atal Incubation Centre and NITI Aayog. With the help of the given facilities, the University’s team were able to conceive and design a solution for the face shield needs following the COVID-19 outbreak.