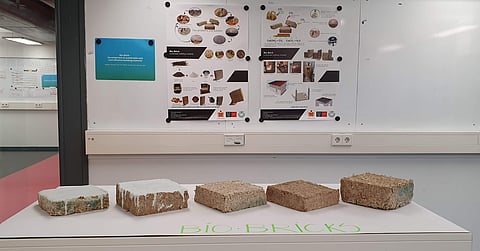
Bricks from sugarcane? How about that for a great idea. Researchers from Indian Institute of Technology Hyderabad and KIIT School of Architecture, Bhubaneshwar, have developed bio-bricks for construction from agricultural waste products. Their development serves the dual purposes of waste management and development of eco-friendly, sustainable building materials.
This research was undertaken by Priyabrata Rautray, PhD scholar, Design Department, IIT Hyderabad and Avik Roy, Assistant Professor, KIIT School of Architecture, Bhubaneshwar and were guided by Prof Deepak John Mathew, Head, Design Department, IIT Hyderabad and Dr Boris Eisenbart from Swinburne University of Technology, Australia.
Explaining how it works, Avik Roy, Assistant Professor, KIIT School of Architecture, Bhubaneshwar, said, “Bio-bricks are not only more sustainable than clay bricks, but are also carbon sinks because they fix more carbon dioxide than they produce during their lifecycle.” The team’s bio-brick received a Special Recognition Trophy for sustainable housing at Rural Innovators Start-Up Conclave 2019 organised recently by National Institute of Rural Development and Panchayati Raj (NIRDPR), Hyderabad.
Priyabrata Rautray, PhD Scholar, Design Department, IIT Hyderabad
Cut that carbon footprint, Mr Mason
Speaking about the need for ‘bio-bricks,’ Priyabrata Rautray, PhD Scholar, Design Department, IIT Hyderabad, said, “As much as 22 per cent of India’s total annual CO2 emissions is by the construction sector. Clay bricks, for example, not only use up fertile topsoil, but their manufacturing process also emits significant amounts of carbon dioxide into the atmosphere.”
Repurposing of agricultural wastes is particularly important in India. More than 500 million tons of agricultural waste are produced in the country every year. While some of this is reused as fodder, 84 to 141 million-tons are burnt, which results in severe air pollution.
For example, the research team used 900 grams of sugarcane bagasse to make a single block. Burning this amount of the waste bagasse instead of repurposing it, releases 639 grams of carbon dioxide. Not only is this release prevented in the making of bio-bricks, but the lime in each brick also absorbs 322.2 grams carbon dioxide from the air during curing, which makes it a carbon-negative or environmentally sustainable.
The bricks being heat tested
How are these bricks made?
Careful selection of the dry agro-waste like paddy straws, wheat straws, sugarcane bagasse and cotton plant
The team decided to use dry sugarcane bagasse for the first sample. The bagasse is first chopped to the desired size
A lime-based slurry is prepared, and the chopped agro-waste is added to the slurry and mixed thoroughly by hand or mechanical mixer, to create a homogenous mixture
This mixture is poured into moulds and rammed with a wooden block to make a compact brick
These moulds are left to dry for a day or two, after which the sides of the moulds are removed, and the brick is allowed to dry for fifteen to twenty days
It takes approximately a month’s time for these bio-bricks to attain its working strength by air drying.
Are they just as strong?
Although these bio-bricks are not as strong as burnt clay bricks and cannot be used directly to build load-bearing structures, they can be used in low-cost housing with combination of wooden or metal structural framework. Besides, these bricks provide good insulation to heat and sound and help in maintaining humidity of the buildings, making these houses suitable for hot-humid climate like India. “Other than as bio-bricks, this material can be used as panel boards or insulation boards and designers we could explore such applications for this sustainable material,” added Rautray.