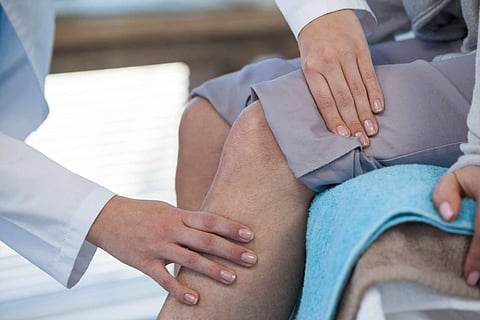
IIT Roorkee researchers have invented a novel technique to address localised and long term drug release for areas that are prone to post-surgical infections that often arise in joint replacement procedures.
Biomedical grade implants are widely used in an orthopaedic procedure to replace damaged or diseased bones. However, a common hurdle faced during these surgeries is that of bacterial infections at the implant site. Approximately 10% of bone implants lead to failures due to diseases. High doses of medications are given to overcome this. Researchers at IT Roorkee have come up with a novel method to deal with this after effect of biomedical grade implants and minimize the chances of bacterial infections at the implant site. This method will modify the surface of metallic implants and load them with an antibacterial drug, which is released gradually over a period of one week or more at the implant site to prevent infections. The medicine was embedded into a micro-layer of hydroxyapatite coated on the surface of biomedical grade titanium alloy metal. HA provided the pores for the drug loading along with facilitating bridging of the bone and the implant.
Speaking on this occasion Dr Debrupa Lahiri, lead researcher, said “Our surface-modified implant is novel technique that addresses localised and long term drug release for areas that are prone to post-surgical infection that often arise during joint replacement procedure. The modified implant surface serves for both drug delivery and bone integration and is on its way for an Indian patent.” By using the plasma spray technique, a 200-micron thick layer of hydroxyapatite was coated on a titanium metal alloy sheet. HA is biocompatible material with a bone-like mineral composition and used in ceramic implants. A commonly used drug gentamicin was mixed with biodegradable polymer called chitosan. Then the drug-loaded polymer liquid was impregnated into the pores of HA under vacuum. Chitosan degrades at the implant site slowly and naturally under the influence of body fluids, thereby releasing the loaded drug. The drug forms a protective layer to arrest bacterial growth.
The team found that the polymer-HA combination had an added benefit: it improved the impact resistance of the implant by 42%. Laboratory tests demonstrated that the modified implant material exhibited excellent antibacterial action against S. aureus, a common bacteria usually responsible for the majority of implant-related infections in orthopaedic surgery. Also, tests on human osteoblast cells revealed that the HA in the modified surface facilitated biocompatibility by bridging the bone and implant to promote bone regeneration.
She also added, “The advantages of such localised gradual drug release are that smaller amounts of the drug can be used avoiding full-body exposure to the medicines thereby facilitating a better control over the toxicity. The gradual release ensures to arrest bacterial infections throughout the healing period. While the next stage of testing procedures is underway, the team is in parallel working on introducing combination drugs into the polymer and extending the drug release period up to one month”,
This interesting innovation was carried out in collaboration with Prof. Partha Roy and his group at IIT Roorkee and Prof. Arvind Agarwal and his group at Florida International University, USA. The other researchers involved in this work are Dr Manoj Kumar R and Kanike Rajesh.